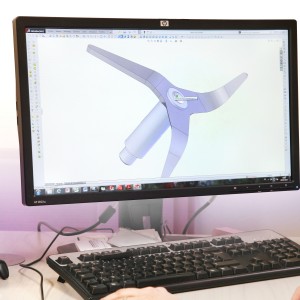
Product features and industrialisation depend upon this stage. Adiamas can work from models prepared by the client, but is particularly skilled at developing cutting accessories based on clients’ specifications. By applying our expertise in working with stainless steel and various assembly procedures (welding, screwing, riveting, moulding, etc.), we use our CAD (computer-aided design) tools to draw, simulate, test and prototype clients’ products to provide them with tailor-made assistance at the earliest stages of creating a product.
This is a crucial stage because good design enables our clients to optimise their costs (in terms of the cost of items and investments) and reduce production time. It also ensures the sustainability of a functional outcome over time. The ADIAMAS™ design department works with Solidworks 2015 to create 3D designs. This software tool is particularly suitable for designing mechanical items such as those offered by ADIAMAS™.
Our CAD software allows us to import and export:
- ‘.IGS’ 3D files
- ‘.DXF’ and ‘DWG’ 2D files
- ‘.X_T’ and ‘X_B’ (native PARASOLID) 3D files;
- ‘.STL’ 3D files
- ‘.STEP’ 3D files
- ‘.VDA’ 3D files
- ‘.WRL’ 3D files
The ADIAMAS™ design department also uses software to calculate the resistance of materials.
Working from this 3D file and taking into account environmental information about the end product (rotation speed, blocking zones, etc.), we can use the simulation software to represent the constraints and distortions affecting the product in question.
This simulation enables us to accelerate the design phase by ‘skipping’ the prototype phase and anticipating and detecting any product faults.
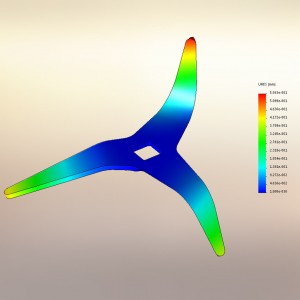